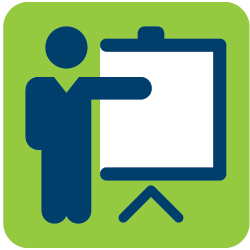
Current offerings of this course
For assistance registering or to bring this course onsite to you, contact ISA Customer Service info@isa.org or +1 (919) 549-8411
Data do curso | Local do Curso | Preço de Tabela/Preço para Membro | Registro |
---|---|---|---|
Monday, Oct 9, 2023 to Friday, Oct 13, 2023 | Houston Kenexis - Houston TX USA | 4450 USD/3560 USD | Registre-se |
ISA Automation Engineering Survival Training (AEST)
Do you have what it takes to survive in the world of process automation?
Sharpen your process automation know-how with this intensive week of expert-led lecture and hands-on exercises covering practical, real-world automation survival skills.
Automation Engineering Survival Training is a unique process automation engineering experience designed to hone your process automation knowledge and skills. This intensive technical training boot camp for automation engineers combines lecture and hands-on labs with bonus features, including a plant tour to maximize your learning experience.
ISA’s seasoned “Survival Expert” will guide you through a fast-paced and rigorous course of topics from process measurement fundamentals through advanced automation, and everything in between! This course also serves as a solid introduction to other ISA engineering courses that can assist in the advancement of your process engineering career.
Who Should Attend?
- New automation, control system, or process control engineers
- Recent process engineering and other engineering graduates
- Seasoned engineers looking to refresh their process automation knowledge and skills
- Individuals wanting to learn more about process automation
Intensive Hands-On Training Curriculum
Days: 4.5
CEUs: 3.6
PDHs: 36
DAY 1: Measurement Basics & Documentation
You Will Cover:
- Concepts of Process Control: Typical Industries | Definitions | Continuous vs. Batch | Feedback Loop
- Documentation: Instrument Line Symbols | Function Symbols | Identification Letters | Piping and Instrumentation Drawing (P&ID) | Loop Diagram
- Industrial Measurement Systems: Process Measurement | Standard Signals | Instrument Performance Terminology | Repeatability and Accuracy | Zero, Span, and Linearity Errors | Calibration Chart
- Control System Hardware: Pneumatic Controller | Electronic Controller | Single Loop Controller | Distributed Control System (DCS) | Programmable Logic Controller (PLC) | Personal Computers (PC) for Control
- Temperature Measurement: Temperature Scales | Liquid-in-Glass, Filled Bulb, and Bimetallic Thermometers | Resistance Temperature Detectors (RTDs) | Reference Junction Compensation | Thermocouplers
- Pressure Transducers: Pressure Elements | Signal Generation | Pressure/Force Relationships | Selection
- Flowmeters: DP | Magnetic | Mass | Other
Classroom/Laboratory Exercises:
- Develop diagrams for flow, level, temperature, and pressure loops
- Interpret simple P&IDs
- Evaluate level instrument performance and accuracy
- Determine upstream and downstream piping considerations
- Select flowmeters for a variety of specific applications and specify installation and calibration requirements
You Will Be Able To:
- Discuss the role of measurement and control in industrial processes
- Differentiate between continuous, batch, and discrete control
- Discuss the fundamentals of process control
- Apply specific ISA Standards to interpret symbols and drawings associated with process control documentation
- Discuss and apply the most common methods and devices used in temperature, pressure, level, and flow measurement
DAY 2: Control Valves & Strategies
You Will Cover:
- Introduction: Valve in Loop | Valve | Actuator | Positioner
- Basic Valve Types: Globe | Ball | Plug | Butterfly
- Installation: Performance | Safety | Other
- Valve Sizing: Manual | Computer
- Review of Feedback Control Concepts and Components: History of Control Operation | Concepts
- Control Modes: Proportional | Integral | Derivative
- Dynamic and Steady State Considerations: Gain | Dead Time | Time Constant
- Tuning Control Systems: Closed Loop Tuning Using Ziegler Nichols Method | Evaluation and Control Criteria
- Advanced Regulatory Control: Feedback Penalty | Challenges in Feedback Control | Real-World Control
Classroom/Laboratory Exercises:
- Size valves manually and with software
- Specify valves, actuators, and auxiliaries for specific applications
- Tune feedback control loops via a number of different methods
- Tune using PC-based simulation software
You Will Be Able To:
- Compare various types of final control elements
- Size valves for any flow condition likely to be found in a process plant
- Define the concepts of PID control
- Explain the operation of the components in a closed loop control system including static and dynamic functions
- Use three methods to tune a control system for stated quality control
- Apply the operation and function of ratio control systems
- Identify real-world control problems as the basis of need for advanced control
DAY 3: Safety & Operator Effectiveness
You Will Cover:
- Graphics and Controls: HMI Hierarchy Design | Classes of Displays | Navigation
- Human Engineering: Human Factors in Console Design
- The Common Problems in Alarm Systems
- The Alarm Management Lifecycle
- Location Classification Standards
- Protection Techniques Standards
- Explosion Proof Enclosures
- Intrinsic Safety
- General SIS Design Considerations: Design Life Cycle | Separation of Control and Safety
- Failure Rates and Modes: Safe vs. Dangerous | Failure Mode vs. Technology | Failure Rates | Test Intervals
- System Technologies: Pneumatic | Relays | Microprocessors
- Operations and Maintenance: Installation | Bypassing | Testing
Classroom/Laboratory Exercises:
- Alarm prioritization
- Area classification
- Calculate device failure rates
You Will Be Able To:
- Design a graphical hierarchy for navigation
- Explain best practices in HMI
- Develop an Alarm Management Philosophy
- Discuss rationalization, classification, and prioritization of alarms
- Describe and use procedures for electrical classification
- Describe the basic principles of protection
- Select explosion proof apparatus for specific applications
- Select the appropriate protective techniques for different hazards
- Differentiate between process control and safety control
- Analyze the performance of different logic system technologies
- Specify and select safety instrumented systems (SIS)
DAY 4: Industrial Security & Project Management
You Will Cover:
- What is Data Communications?: ISO/OSI Reference Model | Terminology Basics
- TCP/IP Basics: Is Ethernet Ready for the Plant Floor? | Industrial Ethernet Design Techniques
- Data Exchange: Using OPC for Inter-System Data Exchanges
- How Cyberattacks Happen: Understanding the Threat Sources | The Steps to Successful Cyberattacks
- Standards and Models: ANSI/ISA95 Standards | MESA International Model | WBF B2MML XML Schemas
- Information Model: Production Resources | Process Segments | Product Definition and Capability | Production Schedules | Production Performance
- Types of Projects: Facility Update | Addition to Existing Process | Technology Replacement | New Facility
- Fundamentals: Activity/Phase Concept | Best Practices | Phase Interaction | What to Do/How to Do it | Do it
- Project Development: Schedule Preparation | PERT | CPM | GANT | Cost
Classroom/Laboratory Exercises:
- Conduct security threat analysis
- Identify key business processes and objects
- Identify process segment definitions
- Practice project scheduling techniques
You Will Be Able To:
- Identify Local Area Network (LAN) topologies and protocols
- Define the different Ethernet varieties and which are best for industry
- Discuss the principles behind creating an effective long-term security program
- Define the basics of risk and vulnerability analysis methodologies
- Specify the requirements for an enterprise-control integration solution
- Explain the business drivers involved in integration
- Identify project types and overall goals and objectives
- Explain the four important objectives critical to automation projects vs. the three objectives typical of other projects
DAY 5: Advanced Process Automation
You Will Cover:
- Physical Model: Process Cells | Units | Equipment Modules | Control Modules
- Recipe Information Categories: Header | Procedure | Formula | Equipment Requirements
- Procedural Control Model: Procedure | Unit | Operation | Phase
- Modes and States: Exception Handling | Allocation and Arbitration
- Control Activity Model: Recipe Management | Production Planning and Scheduling | Production Information Management | Process Management | Unit Supervision | Process Control | Personnel and Environmental Protection
- Integration: Communications | Manufacturing Execution System (MES) | Network Security
- Workflow and Project Leadership: Opportunity Identification and Project Justification | Communications and Team Processes
Classroom/Laboratory Exercises:
Develop procedural elements using the ANSI/ISA88 procedural control model and test those procedural elements against the equipment entities
You Will Be Able To:
- Specify the requirements for a batch control system
- Effectively structure and subdivide equipment entities
- Describe modes and states and how they are applied at the equipment level
- Describe the interfaces that are needed between batch control and other systems within an enterprise
- Apply the critical areas of automation opportunity identification and project justification
- Interpret the best practice methodology for automation project execution